Fulfillment center vs. logistics warehouse

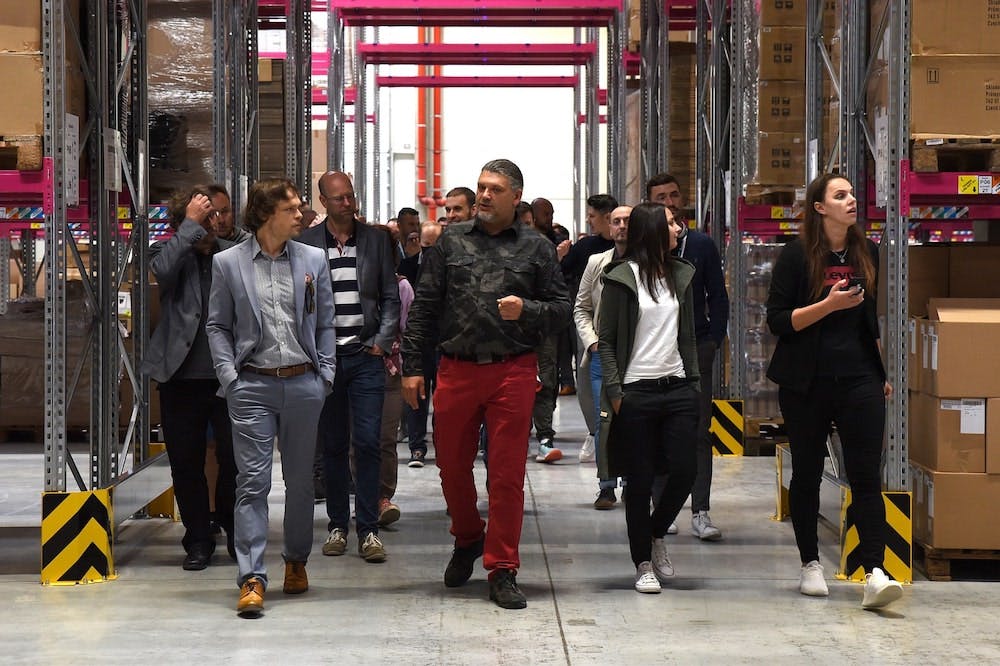
The terms “warehouse” and “fulfillment center” are very often used interchangeably. Yes, both terms refer to a large building in which a certain flow of goods and inventory takes place. But how do these terms differ? What internal processes, other than warehousing, take place in a fulfillment center? Take a look at how to distinguish between a warehouse and a fulfillment center.
Warehouse
As the name implies, a warehouse is a place where products are intended to be stored in bulk for an extended period of time. Here you will find, for example, a fleet of forklifts, shipping containers or high pallet racks that are filled to the ceiling. Literally every cubic meter is saved here. As a rule, this is where surplus or currently unwanted goods are stored.
Fulfillment center
In contrast, a fulfillment center is a facility where 3PL companies (also known as fulfillment providers) handle the goods of their e-commerce clients. The main goal of a fulfillment center is to deliver orders to the client’s end customers (B2C) or business partners (B2B) as quickly and efficiently as possible. It is a facility that completely relieves e-commerce entities of the worries of a key area of their business – logistics.
When you, as an online store owner, decide to entrust everything to a fulfillment partner, you are handing over responsibility for all intralogistics processes in addition to the responsibility for transporting packages. A professional fulfillment partner will help you, for example, to optimize your inventory management or to secure favorable rates from carriers. All benefits can be found here.
The main differences between a warehouse and fulfillment center
There are a number of differences between these facilities, but the following are the most relevant for us.
1. Long-term vs. short-term storage
The role of a warehouse is to store products, while the role of a fulfillment center is to efficiently handle products and thus meet the requirements and expectations of end customers and their partner online stores. The online store should only store the inventory needed for the current demand, ideally for no longer than one month – then it overpays for storage unnecessarily. Fulfillment center require faster inventory turnaround.
2. Implemented processes
Compared to a warehouse, where the environment is more static and less active, there is continuous movement in the fulfillment center. The operations carried out are much more complex, providers offer, beyond warehouse operations, a range of fulfillment services, such as:
- Inventory receiving
- Product picking
- Product assembly and kitting
- Packing of products
- Labelling of shipments
- Ordering transport
- Complaints and returns management
- And much more
3. Frequency of parcel pick-ups
Since the fulfillment center handles orders immediately upon receipt and tries to deliver packages to customers in the shortest possible time, it schedules at least one pickup per day. Fulfillment companies typically work with multiple carriers to be able to deliver packages to their destination at the lowest possible cost. Fulfillment center always have set times for the last order, i.e. an order that will be shipped the same day.
In contrast, warehouses have scheduled deliveries that are less frequent. In these collections, a large number of goods are transported at once, making the movement of goods more cost-effective but not time-flexible.
Conclusion
Effective inventory management is the core of success for your online store. The need for storage space is different from the need for complete fulfillment services. Therefore, differentiate between the terms “warehouse” and “fulfillment center” to choose a truly suitable partner for your business. Is it worth outsourcing your logistics? Download our e-book or calculator to find the answers to this and other questions!