Fulfillment: Picking methods, their (dis)advantages and recommendations

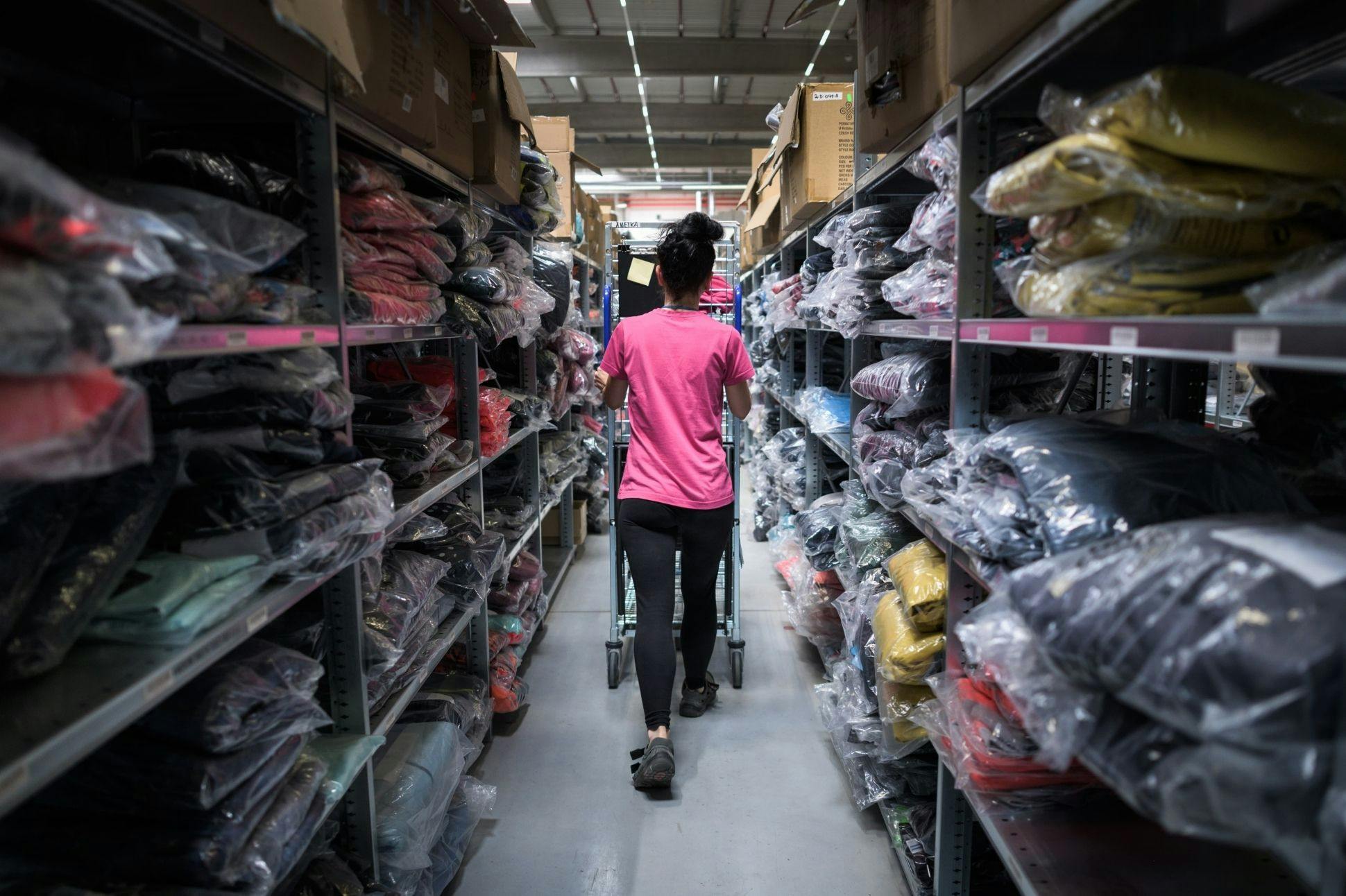
The share of e-commerce in retail is growing steadily, in the Czech republic already exceeding 16% in 2020. To become a strong player in the market, e-commerce needs to respond to this trend. How? There are a number of factors and one of the key indicators is undoubtedly the speed of delivery of goods to end customers. Speed can be achieved in logistics by investing in modern technology, WMS or warehouse equipment, but it is also important to optimise intralogistics processes, including the picking process in the warehouse.
In our article you will learn why the picking process is important, what methods exist, including their advantages and disadvantages or our recommendations for making it more efficient.
What is goods picking?
This is the process of taking products from stock based on system-received customer orders. After picking process follows the process of packing and shipping.
Why is important quality in the picking process?
If you have the picking process set up correctly, you increase your fulfillment level. Your orders are processed faster and with a low error rate which ultimately affects the satisfaction of more than just your customers. Systematic picking brings the following benefits:
1. Reduction of logistics costs
The larger the warehouse the more costly is low quality picking process. That’s why we recommend investing in an appropriate warehouse management system (WMS) when your e-commerce business grows significantly. It completely manages the operations in the warehouse, brings automation, has useful features and provides data for further improvement. In the case of picking, it merges multiple related orders into one dispatch*, determines optimal routes or product placement according to turnover rates in zones, etc. When used correctly, you will achieve significant time and cost savings.
* List of products (including their quantity and location) that need to be picked by warehouse staff (pickers)
2. Increase customer satisfaction
The delivery of goods directly affects the satisfaction of customers who appreciate the timely and content correct delivery of their orders.
Picking accuracy is an important metric for e-commerce logistics. Just to give you an idea, the independent server fulfillmentcompanies.net reports that the average picking accuracy is 99.51%. The speed and accuracy of a shipments determine the number of subsequent customer support inquiries, verbal and online reviews, and the number of complaints or returns. They affect customer lifetime value (CLV), i.e. loyalty and the likelihood of repeated future orders.
3. Higher productivity of warehouse staff
The implementation of a function optimal picking routes with their constant updating reduces the picking time per item. A quality WMS also minimizes the space for human error.
Picking methods in the warehouse
As already mentioned, the picking process is an important part in the supply chain. The choice of the optimal method is influenced by a number of variables, such as the size of the warehouse, the number and nature of products stored, the total number of your employees, etc. Below are the 4 most common picking methods.
1. Picking per 1 order
The simplest method where the picker picks the complete order across the entire warehouse. Usually picks orders chronologically according to their receipt into the system.
This method is suitable for orders with a high number of items or SKUs. Compared to the others it requires much more movement and therefore warehouse staff time. It makes sense until the “limit capacity” in the number of orders is reached. Then you need to switch to one of the following methods.
2. Batch picking
This is the most suitable option if the individual orders contain the same or similar SKUs. These orders are merged into a single dispatch and the operation staff visits the warehouse area only once.
Typically, it is used for orders that contain only a few products and their dimensions are relatively small. For example – they can fit into boxes in a transport trolley. The aim of this method is to increase productivity. The warehouseman minimizes the length of the routes.
3. Zone picking
Each picker operates at a specific area of the warehouse for which they are responsible and from which they pick goods for all orders. If products from different areas are included in order, this order is picked successively by several pickers. Order processing is thus similar to an “assembly line” also referred to as “pick & pass”.
This method is suitable for complex operations that process a higher number of larger orders with different items. A necessary is the adaptation of the warehouse layout into so-called zones, e.g. according to the turnover of products or their character. The advantage is the assumption of increased picking accuracy. Each picker operates with the same products in a given area. The disadvantage can be time collisions due to different capacity of each zone.
4. Wave picking
It can be processed by any of the above mentioned methods or its combination. The picking is scheduled on a period basis into so-called optimal waves, i.e. planning slot for picking specific orders according to set priorities, conditions or capacities. This method takes into account the current distribution of goods in the warehouse, available manpower, delivery times, required dispatch dates, carrier pickup times, etc. The aim is to maintain the maximum SLA* and capacity utilisation of the carriers.
* SLA = Service Level Agreement, i.e. the level of service provided. It is influenced by e.g. compliance with the shipping deadline, accuracy of picking goods, etc.
Picking recommendations
The chosen method of picking needs to be constantly improved, to be as effective as possible. Below are some recommendations on how to achieve gradual optimization.
1. Use WMS
A suitable WMS automatically generates dispatches according to the selected method, displays the exact quantity of stock, alerts the need to reorder products, provides real-time statuses of all orders, helps with shift planning, etc. For a complete list of recommended warehouse system features, please see our WMS checklist which you can download here.
2. Use appropriate storage equipment
Invest in equipment that is safe, makes the process easier and ideally brings automation. Whether it is equipment like boxes or trolleys, shelving, order sorting systems, barcode scanners and other IT hardware. Make sure that the individual pieces of equipment are compatible with your warehouse system.
3. Optimize the warehouse
Fulfillment is composed of several logistical processes that take place simultaneously. Therefore, you need to continuously optimize your warehouse. Update stock positions according to current needs, shorten picking routes or ensure smooth transfer of picked goods for packaging.
4. Monitor warehouse productivity
Focus on your staff and continuously improve their skills and competencies. Communicate and motivate your warehouse staff to increase their productivity. Check data on inventory turnover, dispatch times, average warehouse capacity used and of course accuracy in order picking. Use a WMS. Discuss the results and look for improvements.
Fulfillment without worries
As e-commerce grows so do the demands on the quality of picking. Picking is an integral part of the fulfillment process and largely influences brand perception and builds customer relationships. In short, it can greatly impact your business so you need to constantly push it forward.
Of course, you can build quality logistics yourself but it is a long, never-ending and costly process. On the other hand you can take advantage of the know-how of a competent fulfillment expert who has already fine-tuned the logistics. What to look out for when choosing one? Download our guide to choosing a fulfilment partner.
As usual, every change brings with it a number of advantages and disadvantages. The same is applicable when outsourcing logistics to an external partner. You will find an overview of these in our next article “Fulfillment: Advantages and disadvantages of logistics outsourcing“. We wish you good luck not only in choosing the right picking method!