E-commerce logistics: How to avoid out of stock

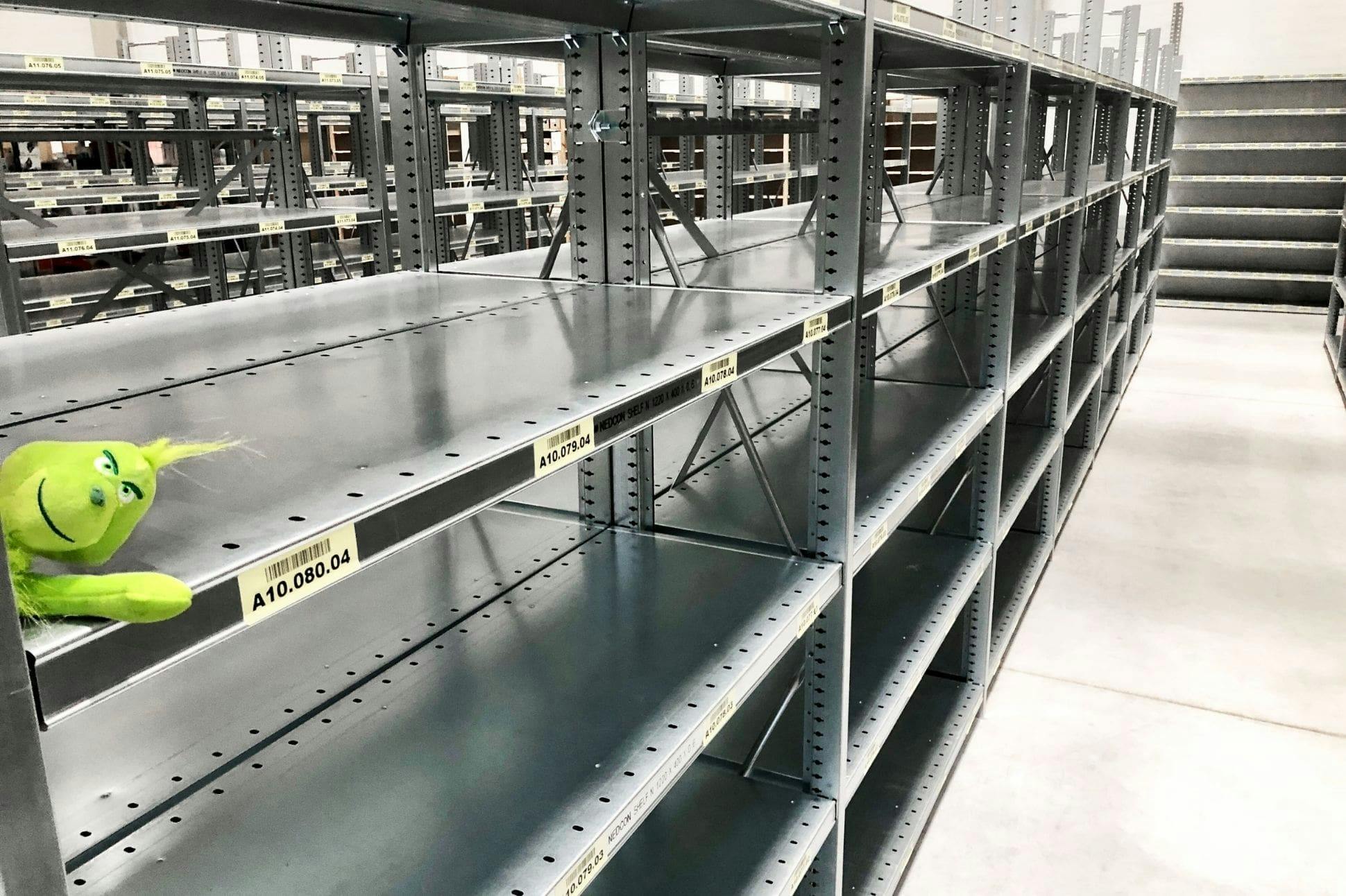
Nothing is permanent in the world. And it’s no different in the e-commerce business. If you have a systematic inventory management set up for your online store, even the best forecasting of future developments may not be enough. Sudden turbulence occurs both in the demand for your products and in the delivery times of your suppliers. And both of these scenarios can result in a common outcome – running out of stock.
A result that causes you to lose both potential profits and your (loyal) customers. Ask yourself – would you have the patience to return to an online store that repeatedly doesn’t stock what you currently need? Especially if you are doing business in a competitive environment?
So how do you put a system in place to help you manage these unexpected changes? The answer is safety stock. Try to be the ones who build windmills when the winds of change blow, not the ones hiding in shelters.
What is a safety stock?
The safety stock is a cushion in the inventory which, with proper inventory management, helps to cover orders during the above mentioned non-standard situations – i.e. unexpectedly increased demand or extended delivery time. It is therefore a solution for emergencies or temporary failures in your supply chain.
In layman’s terms, it is an ‘just in case’ stock that may appear to be redundant due to higher storage costs. However, this is only the case if your insurance stock is truly oversized. So how do you find the right level of safety stock?
By calculating the optimum size of the safety stock, you will find out how many units of a given product you need to keep in stock to keep the associated costs as low as possible, but also to be able to handle the maximum number of orders received until the new goods are delivered to your warehouse. At this point, you are working with what is known as the safety stock level*, which contributes significantly to the quality of your logistics service.
* This is the proportion of orders that you are able to clear from your safety stock within a set period of time. For example, with 95% safeting, 95% of orders will be processed, but you will not have enough stock for 5% of orders.
As we noted above, we don’t live in an ideal world where sales and lead times are always constant. If that were the case, the inventory management process would be considerably simpler. Therefore, we will show you how to calculate safety stock.
How to calculate the satefy stock in 4 steps
The size of the safety stock is calculated at the level of individual products (SKUs). In the literature you will come across a number of approaches to calculating the safety stock – whether calculations using the properties of the normal distribution of variances, with demand variability, with supplier delays, etc.
For us, we recommend a simple calculation that takes into account daily product sales and supplier lead times.
So how to calculate your safety stock?
1. Analyze the following information at product level
- Historically maximum daily sales of the product
- Average daily sales of the product over the selected time period
- Historically maximum lead time of the product
- Average product lead time for the selected time period
For average values, take into account current external market influences – demand for your products, supplier capacity, carrier capacity or other relevant context – delays due to holidays, etc. You can use the same period last year as a guide.
2. Set your maximum
This is a scenario where you sell your products at daily highs, but your supplier’s lead time is at its longest. So in both cases, these are historical highs, again at a specific product (SKU) level.
Maximum = maximum daily sales * maximum lead time
3. Determine your average
In simple terms, this is a situation where you are ordering a “standard” quantity of product that will arrive from your supplier within a standard lead time. This average is calculated over the period you choose and again at the level of the specific product (SKU).
Average = average daily sales * average lead time
4. Calculate the safety stock
The last step is to subtract your average from the maximum. With this difference, you will be prepared for the unexpected scenarios mentioned above. As a result, you will minimize the risks associated with selling out of inventory, customers leaving for competitors, or incurring unnecessary financial losses.
Safety stock = maximum – average
Safety stock = (maximum daily sales * maximum lead time) – (average daily sales * average lead time)
Note: An extreme situation may occur where demand or lead time exceeds its previous maximum. In these cases, the likelihood of running out of stock unfortunately also increases. At this point, we recommend that you keep in mind that the next time you order from your supplier, which is likely to be in a shorter timeframe, you need to increase the quantity ordered to replenish your safety stock.
Advantages of using the safety stock
The importance of safety stock becomes even more important in B2C online sales. Customers are particularly used to speed in the delivery of their orders with online stores. In the Czech Republic, next day delivery (D+1) is already well established. If you are not able to provide this standard, it takes shoppers literally a few clicks to switch to a competitor, which is a much faster process compared to brick-and-mortar stores.
That’s why we recommend safety stock management, which brings with it the following benefits.
1. Minimising the risk of stock-outs
The main objective of working with safety stock is to prevent stock-outs. By doing so, safety stock helps you maximize your sales and has a positive impact on both the customer experience with your online store and the lifetime value of your customers.
2. More efficient use of warehouse space
While inventory insurance brings with it increased storage requirements and associated costs, this is only true for standard periods. If you are storing the optimal size of safety stock, these costs are negligible to say the least, considering the benefits mentioned above. To further reduce storage costs, we also recommend grouping the same SKUs into as few storage positions as possible.
3. More flexible inventory management
Working with safety stock offers you a helping hand in forecasting, planning and inventory management if complications arise due to increased demand or delays in lead times from your supplier. It provides “wiggle room” for deviations that arise.
MySkladon: The inventory management assistant
Calculating safety stock is only one piece of the puzzle in inventory management. To minimize the risk of out-of-stocks, you also need to work with other variables such as re-order pont (ROP) and re-order quantity (ROQ).
In this mechanism, the signal inventory level works as an alert that is triggered when the quantity of the stored product drops to / below a set level. It therefore alerts you to the most appropriate moment to reorder stock from your supplier. On the other hand, the optimal batch size informs you, based on a more detailed analysis, about the ideal quantity of goods to order. For a visual representation, we offer the following simplified chart.
* the safety stock is already part of the signal stock level
However, to pick up on the first sentence of this paper, the safety stock, like the signal level of the stock or the optimal batch size, is not constant over time. That’s why it’s important to have a constant overview of your inventory management.
Our clients have this capability in the MySkladon client application. They can thus analyse sales and lead times of their products and are thus able to calculate average and maximum values to determine safety stock or optimal order sizes for their suppliers. The app also offers the setting of signal stock levels for specific products – when these thresholds are reached, users are notified either directly in the app or by email.
Your logistics data is thus available to you in real time, online and 24/7. In other words, in MySkladon you get a useful tool for managing your own stock, which is an important prerequisite for minimising the risk of stock-outs, stability and growth of your business.
“I see the greatest added value in the MySkladon client application in the accurate information about our inventory and the details of individual orders,” Simona Benkova, Process Manager at Skinners.
Skladon: Partner for your growth and logistics without limits
The success of your e-commerce logistics lies in the fact that your customers’ orders are delivered easily, quickly and in the ordered composition. Do you have a goal to maximize sales, improve order handling and provide a superior customer experience that will lead to positive reviews across all channels?
“With logistics outsourcing, it doesn’t matter if you have 100 or 10,000 orders a day. If the process is set up correctly, it is always possible to ship orders without major problems,” Tomas Pokorny, Co-Founder Dogsie.
“Our customers praise the speed of delivery and flawless packaging. We praise the very nice and helpful staff, reliability and communication from Skladon. The icing on the cake is that it is cheaper for us to outsource our logistics than if we handled it internally with our own warehouse and warehousemen,” Martina Kovacova, Co-Founder zKokosu.
Whether you are looking for a solution for your growth or a stable partner for your logistics, join forces with Skladon. Our know-how, established infrastructure or investments will bring your logistics to the level of the biggest local players. Thanks to our warehouse flexibility and broad employee base, we are able to guarantee the required number of warehouse positions and operators purely for your online store needs. In our operation and cooperation we emphasize technology and personal approach not only from our client support… Which are the core and the future of reliable e-commerce cooperation.
See other the stories of our clients
“At Skladon, they always devote maximum energy to the solution, they see the correct setup and functioning as an absolute priority. They realize that emerging collaborations can limit or even jeopardize our business,” Pavel Kovar, Logistics Manager Kilpi.