Inventory shrinkage: How to prevent it?

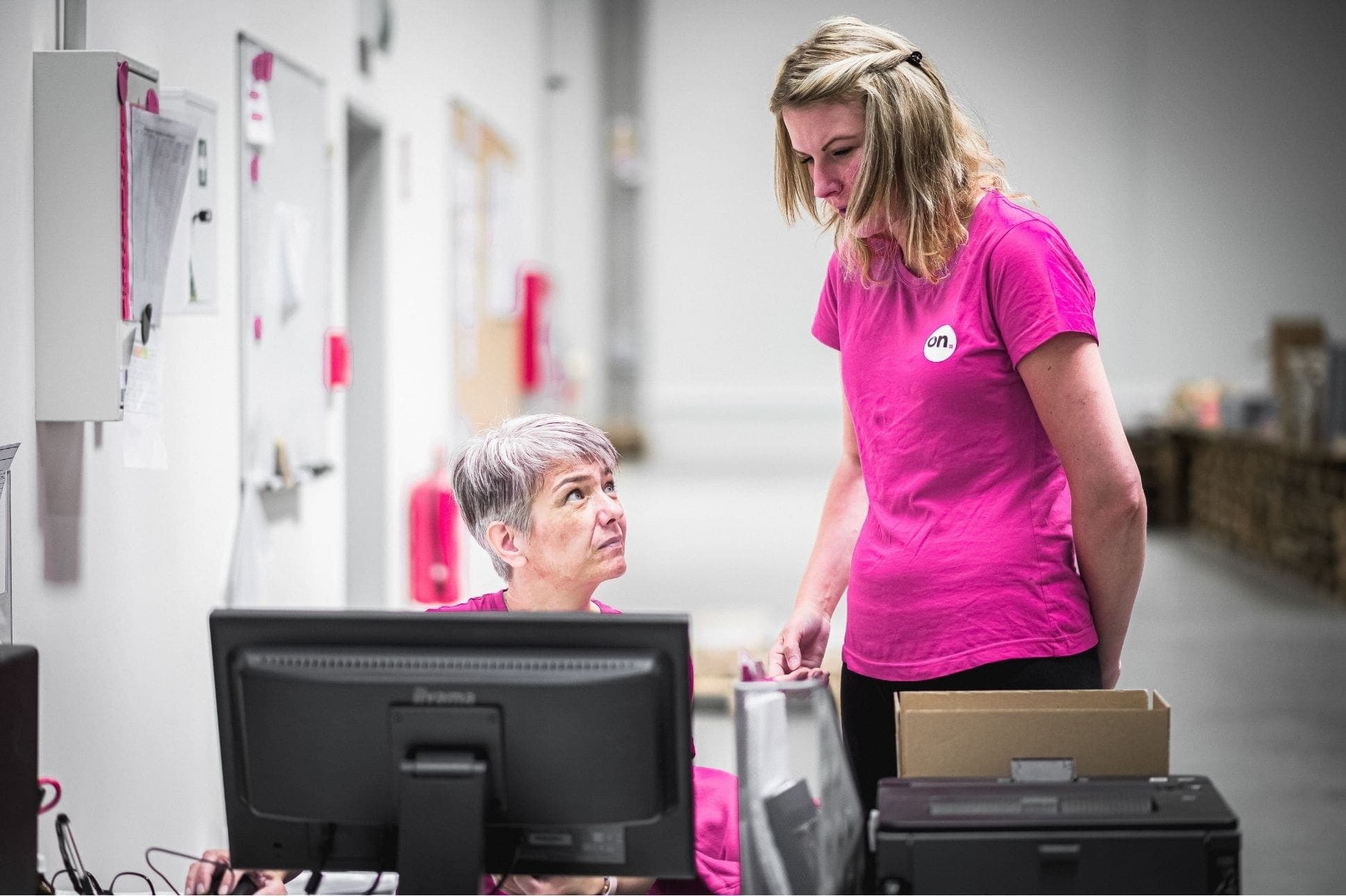
Inventory shrinkage is a very common problem in the operation of online stores. And very often it ends up being a negative combination of two variables – it tends to be unexplained (cause or timing) and always leads to reduced company profits. What’s more, inventory shrinkage is further linked to other mandatory steps, especially in accounting. And incorrect accounting can result in a visit by representatives of the tax office for a financial audit.
What are the main causes of inventory shrinkage and how to avoid it as much as possible?
What is inventory shrinkage?
Inventory shrinkage is a situation when a quantity of products physically counted is lower than a quantity recorded in a system. The current stock level is determined during a physical inventory, and differences between the actual and the accounting stock levels are called inventory shortages or surpluses, and these differences cannot be documented, explained or proved. The following diagram illustrates the inventory process and possible results.
* Shortages up to determined level – an entrepreneur operating retail sales may also include here unexplained shrinkage (theft in stores), or natural shrinkage (expired goods), etc., according to rules established by law.
From an accounting point of view, each type of inventory must be inventoried at least once per accounting period; verification is usually carried out at the closing date, but may be carried out on a continuous basis. In the case of a similar product type, surpluses and shortages of individual products may be confused and these confusions must then be justified and documented.
How to calculate the inventory shrinkage rate
The inventories shrinkage can be expressed in relation to the current accounting value. To calculate the inventory shrinkage rate, we recommend the following formula:
Inventory shrinkage rate = [(inventory in accounting – actual counted inventory) / inventory in accounting] * 100
Let’s illustrate how the formula works with a practical example.
You own an online store and the accounting value of your inventory is EUR 5941.63. You have just completed an inventory of the stock actually held in the warehouse and you have concluded that the current value of the stock is EUR 5347.47.
The result of the inventory shrinkage rate for this example is:
Inventory shrinkage rate = [(5941.63 – 5347.47) / 5941.63] * 100
Inventory shrinkage rate = 10%
The result therefore tells us that the online store lost 10% of the value of its inventory due to shrinkage.
The main causes of inventory shrinkage
Inventory shrinkage occurs for a number of reasons and preventive measures need to be set up to eliminate it. Of course, the degree of causes differs when you own a purely online store or you also run brick-and-mortar stores in addition to the online store. According to SheerID’s research, the causes of inventory shrinkage are as follows:
- Employee theft: 42.7 %*
- Shoplifting: 35.6 %
- Administrative: 15.4 %
- Vendor fraud: 3.7 %
- Unknown: 3.9 %
* According to other available research, retail theft by store employees is up to 70%.
Theft by employees with access to storage spaces
Your employees, especially those operating in the warehouse, have almost continuous access to your inventory. According to the aforementioned research, thefts from this channel cannot be overlooked. We recommend installing trail cameras or permanent devices with camera recordings, building lockable cages for expensive products with restricted access for some of employees, electronic detection gates, or implementing personal checks when leaving the warehouse, checks when disposing of waste, restricting access, or controlling the movement of unauthorized persons in storage areas (e.g., carriers), etc.
Theft by customers
These are classic thefts in brick-and-mortar stores. Measures may vary depending on the products sold; expensive products can be displayed in lockable showcases, equipped with ink or electronic tags, RF self-adhesive labels, and more. Generally, it is also recommended to introduce physical security, electronic attendance tracking, security doors and windows, various sensors and detectors, etc.
Depreciation
These are products that have become unsellable for a specific reason. This can include mechanical / chemical damages, or its packaging, expiration of product, etc.
Administrative errors
These typically involve human errors. Incorrect record-keeping (whether internal or elsewhere in the supply chain), inventory discrepancies, improperly used methodology or units of measurement, etc. It’s worth noting that companies don’t rid themselves of errors even with the introduction of full automation.
7 ways to prevent inventory shrinkage
There are several ways to eliminate inventory shrinkage. For even higher effectiveness, we recommend combining individual methods.
Item tracking
Label individual products, especially those with long-term high rates of inventory shrinkage, with security tags. Whether they are ink, magnetic, or electronic, this allows you to better track whether goods are disappearing from your warehouse or brick-and-mortar store.
More frequent inventories
To reduce inventory shrinkage, it’s advisable to conduct inventories more frequently throughout the year. To speed up the process, we recommend inventorying individual sections of your warehouse separately (known as zone inventory) or conducting more frequent inventories of expensive and sensitive items. Use software during inventory that allows for real-time updating of inventory levels and avoid applications like Excel that are not automatically synchronized with the inventory system.
Random inventories
Do not announce inventories to your employees in advance. Conduct them randomly and unplanned in their presence. By doing this, you give your employees less time to prepare, making it possible to quickly detect anomalies in quantity levels.
Increased security measures
Try to ensure the highest level of security for your premises – both for your warehouse and brick-and-mortar stores. There are a variety of options, from physical security guards to camera systems to lockable equipment. It is also recommended to use transparent waste bags to reduce the risk of merchandise being taken outside your space.
Allocation of responsibilities
Ideally, each job position should be doubled. Among other benefits, this also prevents a decrease in fraudulent practices, the risk of which increases when only one employee is responsible for specific tasks. Establish mutual checks and documentation among employees, and rotate task delegation within specific job positions.
Building company culture
Make your employees aware of how inventory shrinkage (in)directly affects them. Discuss its impact on their promotions, salaries, profit shares, etc. Communicate openly with your employees, invest in their education and career advancement, offer benefits (such as bonuses tied to inventory results), organize team-building events, etc. Cultivate a maximally positive relationship with your, or “their,” company.
Collaboration with a fulfillment partner
By partnering with a fulfillment partner specializing solely in storage and logistics, many of the above measures are likely already done. Collaboration helps avoid the need to find ideal solutions, often significant investments, and saves time and money that can be devoted to optimizing other areas of your business.
Why collaborate with a fulfillment partner?
At Skladon, we approach our clients on an individual level, being open to conducting inventories at pre-agreed times or only for specific products. By doing so, we avoid sales peaks with clients and ensure smooth processing of their orders throughout the year.
Let’s not kid ourselves, even the world of fulfillment isn’t one hundred percent immune to inventory losses. However, at Skladon, when such situations arise, we respond to our clients by compensating for any damage incurred. We offer discounts for individual warehouse operations or, for example, provide free storage for a certain quantity of products.
Our clients also have the option to manage and oversee their inventory and its flow in the MySkladon application. It offers real-time data and extensive reporting options that help clients efficiently manage their inventory.
Take advantage of these opportunities and have a customized pricing proposal tailored to your needs developed for you. A proposal that you can compare with your current solution. This way, you can achieve significant reduction in your financial costs and boost the expansion of your business.