E-commerce logistics: When to order goods from your supplier?

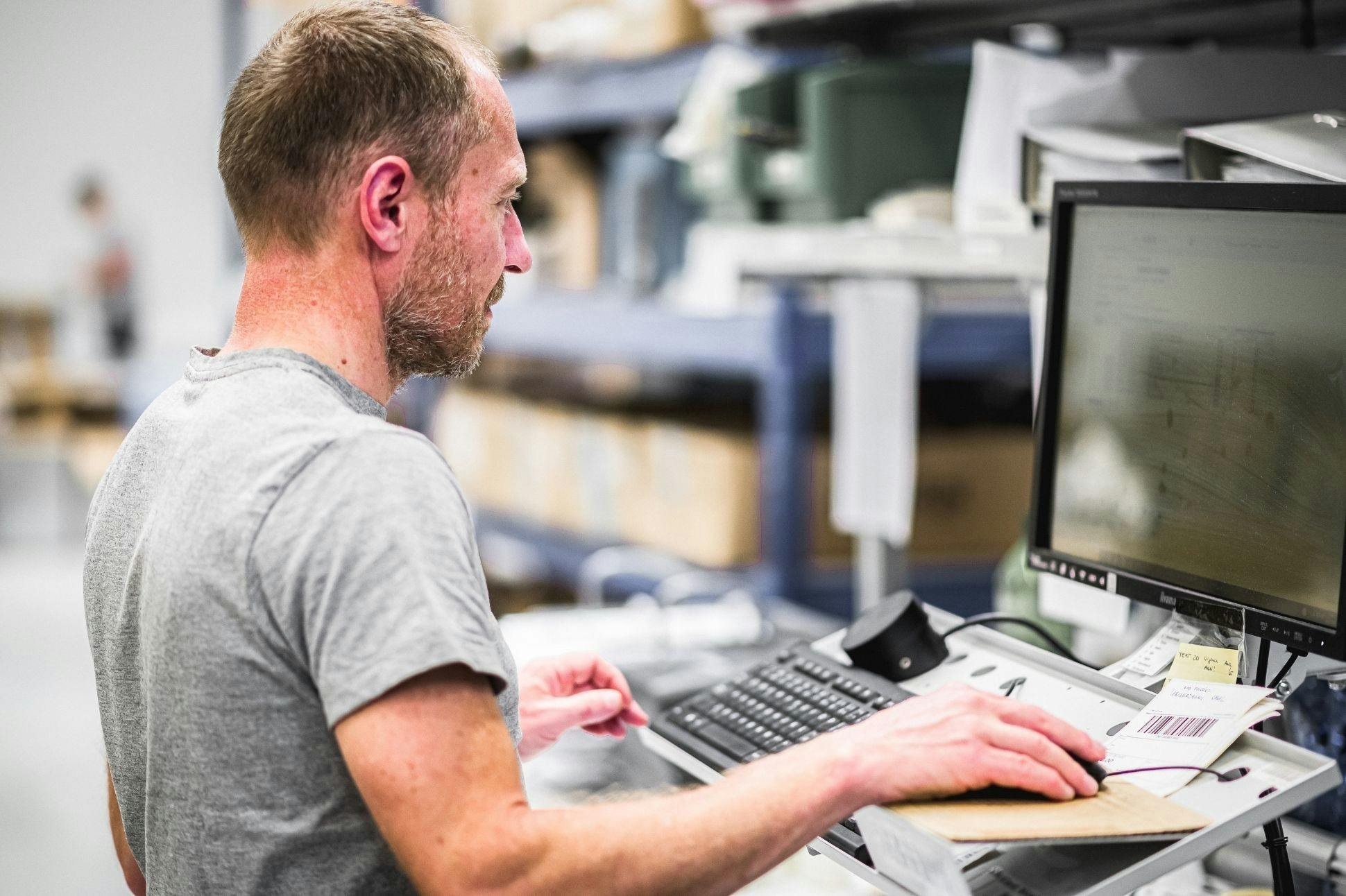
The optimal quantity of goods in stock is the result of efficient inventory management. It depends on a number of factors, including the size of the warehouse space, end customer demand or the reliability and speed of suppliers. Finding “the middle” between oversupplying and adequate stock level is a complex task for any logistics manager.
So how to determine the right time to place a new order with a supplier? A lot of online stores answer this question with “when the goods are out of stock”. This answer may be generally correct but as you can probably guess – insufficient. In logistics is for this purpose used the term reorder point. How to calculate this point, which is unique for each product? What are the approaches and what all can affect it? Read on in our article from the inventory management series.
What is the reorder point?
The reorder point (ROP) is the quantity limit for a particular product at which it is necessary to reorder the goods from a supplier. The calculation takes into account the so-called extended lead time which starts with the notification of the need to order and ends with the delivery of the goods to the online store warehouse. By setting accurate reorder points, the risk of running out of stock of a given product is reduced. Even when the e-commerce business is already waiting for the delivery of new goods.
It is also important to note that reorder points need to be worked with over time. Their value depends on a number of factors such as current seasonality or planned marketing events.
Ideally, the reorder point of each product is defined in the warehouse management system (WMS) which will automatically alert you when the quantity of products falls to / below the set level or is able to automatically generate a new order with your supplier. The question of how many products to reorder also arises in connection with the reorder point. The answer can be found under the term optimal reorder quantity (ROQ).
The importance of the reorder point (ROP) in the replenishment system can be seen from the following simplified diagram.
How to calculate the reorder point
There are several ways how to calculate the reorder point. For us, we recommend this simple formula:
Reorder point (pcs) = Demand during lead time (pcs) + Safety stock (pcs)
In order to add accurate numbers to the formula, two other variables need to be calculated – demand lead time and safety stock.
Demand during the lead time
Lead time is the number of days from ordering products from your manufacturer / supplier to their physical delivery to the online store warehouse. To calculate the demand during the lead time, you need to multiply this number of days by the average daily sales of the specific product.
The formula for calculating the demand during the lead time is:
Demand during lead time = Lead time (days) * Average daily sales (pcs)
Safety stock
Imagine a situation where you have already sent a new order to your supplier but suddenly the sales of the ordered product have increased unpredictably or you are waiting longer than you are used to for the delivery of the goods. And you are at risk of running out of stock. This is exactly the kind of situation for which the so-called safety stock is also used when setting reorder point for goods. In short, these are “just in case” goods.
Safety stock = (Maximum daily orders * Maximum lead time) – (Average daily orders * Average lead time)
The maximum and average values you enter into the formula are obtained from sales records for certain time periods and from your own experience of working with the supplier.
Why is it important to work with reorder points?
By precisely setting the individual reorder points, you take the worry out of managing your own inventory. Specifically, you can achieve:
Reducing the risk of running out of stock
If you operate with low stock levels for individual products, you risk out of stock. Your customers’ orders are delayed, cancelled or not fulfilled at all. In other words, they damage your brand, represent lost profits or lead to customers leaving your business to competitors. In any case, they negatively affect the customer experience with your online store.
Lower costs
Try to store your goods efficiently, i.e. at ideal stock levels. A faster and smoother physical flow of goods in your warehouse will always have a positive effect on your profitability, profit and cash flow.
Improving the supply chain
Correctly setting and working with reorder points has a positive impact on your complete supply chain. The quality of the flow of goods is not only reflected in the route “your warehouse – customer”. Timely communication and delivery of goods to the warehouse is the dream of every supplier or online store.
Data accuracy as a basis for successful business
By setting your own reorder points you can answer the question of when to order goods from your suppliers and minimize the risk of selling out. Ensure your customers are assured of fast delivery of the goods they order.
The primary prerequisite for setting ideal reorder points is an accurate and up-to-date overview of your inventory management. For these needs we highly recommend working with a warehouse management system (WMS). What all should be included in this software? Download our free checklist.
Need advice on inventory management? Are you looking for other ways to streamline your logistics and give your business room to grow? Do not hesitate to contact us.